Ammonia as a refrigerant, a safe choice for a sustainable future in the food industry
The synergy between Soluzione Termica & Frascold
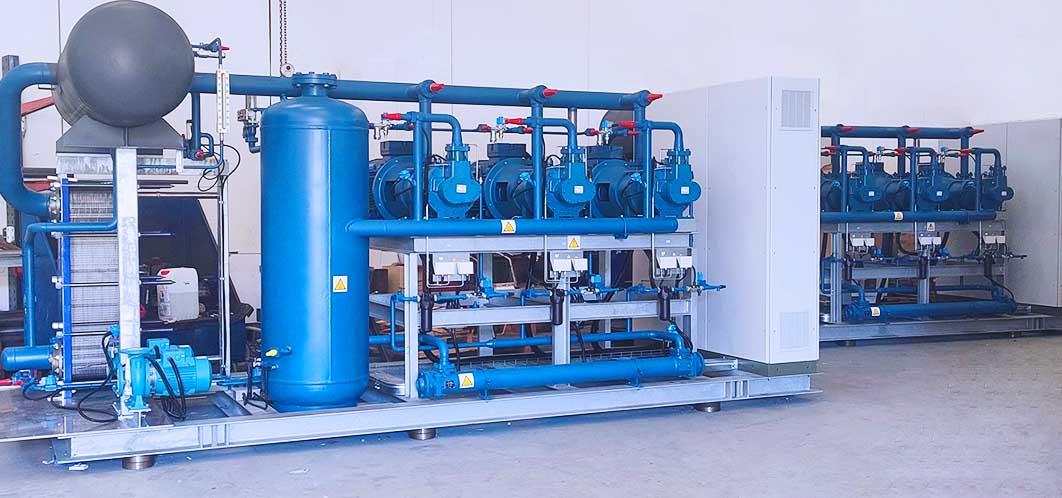
The use of ammonia as a refrigerant and its benefits in industrial refrigeration for the food industry.
Ammonia, among the natural refrigerants, has always been a protagonist in the field of industrial refrigeration. By virtue of the stringent constraints imposed by the regulations for the phase out of F-gases, especially in Europe, this fluid reconfirms its role in numerous markets, primarily in the Food sector.
Appreciated by operators in the food preservation sector for its thermodynamic properties, ammonia, in fact, with a GWP and an ODP equal to zero has all the characteristics for presenting itself as a safe and long-term alternative. Ammonia systems, enhanced in efficiency, are a guarantee of low energy consumption and high yields. Pluses that meet the needs of end users to combine sustainability and excellent performance.
In this context, the Soluzione Termica project was born, which together with Frascold took care of the efficiency of a production site of a leader in gastronomy speciality products and a company renowned in the market of fresh cheeses, mozzarellas and burratas at an international level.
In detail, Soluzione Termica – a player that has been operating for over 30 years in the field of eco-friendly industrial refrigeration – has carried out an in-depth analysis of the Customer’s production processes: from the receipt of milk to the preservation phase of the finished product, to propose an alternative to the systems in operation, composed of cooling units with traditional refrigerant fluids. Specifically:
- it was planned to build two NH3 chillers, with Frascold compressors that will constitute the new refrigerated glycol production plant used both for cooling the premises and for processing.
- The new plant also ensures a controlled temperature of 2/4° C, within the new storage and distribution platform of the finished product of about 25,000 m3.
- The two chillers each consist of three high-efficiency Frascold screw compressors coupled directly to IE3 motors and feature flooded plate evaporators.
Mirco Pasotti, Frascold’s Central and Southern Italy Sales area Manager, said: “One of the main challenges overcome is ensuring the scalability of the groups, in relation to the extreme daily and seasonal variability of the thermal loads. In this sense, a system was required that can always provide an adequate level of power, using sustainable solutions, for an optimal COP (Coefficient of Performance). The choice to opt for three ATSH 360-A series screw compressors derives from the desire to modulate the cooling capacity with high precision. Maximum efficiency at partial loads also depends on the possibility of reducing the number of compressors in operation,according to the cooling demand. A solution that has guaranteed benefits not only in efficiency and environmental impact, but also in terms of energy saving and Total Cost of Ownership.”
Giandomenico Iobbi, CEO of Soluzione Termica states: “We rely on Frascold because it is able to guarantee constant support for the entire project: from the prototyping phase, to the manufacturing of the systems up to the collaboration in the field. It was, therefore, natural to dialogue with their Technical Department in order to identify the most suitable compressors for our customer’s ammonia plant,” and he concludes, “I consider it important to promote the use of NH3 without prejudice. Ammonia offers a solution that is not only immediate and definitive but also proven by long-standing use and knowledge by the market. The regulations relating to “low charge”, although more stringent with regard to safety, are generating favourable conditions for a large-scale use of the fluid, even in new application contexts.”