The first 100% transcritical CO₂ industrial plant in Australia
Signed by Frascold
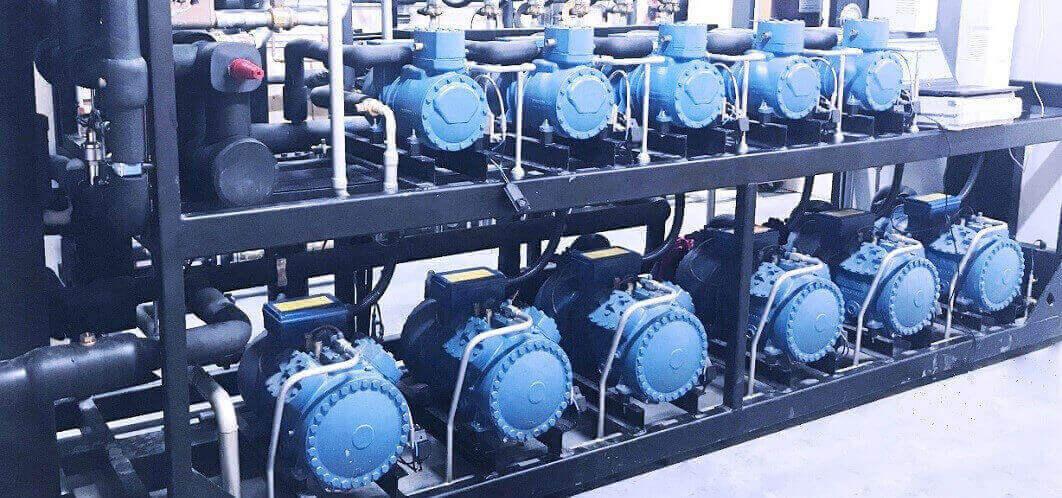
An unprecedented installation, thanks to the application of the transcritical technology.
Frascold contributed to the creation, in Australia, of the first full transcritical CO2 refrigeration system for industrial application, using Frascold compressors at the core of a wider installation, which involved a local wholesaler in the New South Wales. The project included the construction of a wing for the presentation and storage of fresh and frozen products, a meat processing area, a dedicated entrance for sales and a loading-unloading area. In order to effectively meet the needs of the Client, the building was designed using the most advanced technologies aimed at reducing emissions into the atmosphere while preserving the natural resources, ensuring a low environmental impact.
A BREAKTHROUGH IN TRANSCRITICAL TECHNOLOGY
“This is an unprecedented installation, thanks to the application of the transcritical technology in a geographical area characterised by high temperatures. Traditional refrigerants or a combination of CO2 and ammonia are generally the solutions of choice for this type of systems”, says Shaun Hadfield, Managing Director of CRS/Sphere – a South African OEM –, who adds: “In line with Client’s philosophy, oriented towards sustainability, we have proposed an environmentally-friendly yet efficient system, for the best return on investment. The plant fully complies with the provisions of the Kigali Amendment and the Paris Agreement in force in Australia”. He concludes by saying that “Frascold's contribution was decisive, both for the high quality of their solutions and the excellent technical and logistical support provided, which allowed us to brilliantly overcome the limited time constraints dictated by the need to import most of the components”.
THE EXCELLENCE OF AN EFFICIENT SYSTEM
CRS/Sphere’s innovative CO2 booster system, whose installation was handled by the contractor MB Refrigeration, provides numerous advantages. In particular, the plant uses solar energy and, being connected to the HVAC system, it can reuse the heat emitted by the refrigerated counters and cold-storage rooms for water and room heating.
Also, efficiency is enhanced by the additional heat exchanger, by hot gas defrosting, that ensures lower electrical management costs and by the use of parallel compression, incorporated in the solutions offered by Frascold. In detail, the plant uses 11 compressors, delivering a total power of 256 kW (LT 108 kW at -25 °C [-13 °F] and MT 148 kW at -7 °C [-19 °F]).
FRASCOLD'S CONTRIBUTION TO THE PROJECT
In order to deliver the required cooling capacity, Frascold had to take into account the climatic profile of the local area which has high maximum temperatures with peaks of nearly 40 °C (104 °F). With this in mind, Frascold proposed a complete solution consisting of four S 30 18 TK transcritical compressors for medium temperatures, five D 5 11 SK2 subcritical compressors for low temperatures and two S 20 12 TK transcritical compressors with parallel compression. “Parallel compression was the preferred solution since, in hot locations, the RPRV valve (i.e. flash gas valve or medium-pressure valve) operates at high opening levels for a long time, thus forcing the medium-temperature compressors to work harder and with a considerable pressure difference between the intake and exhaust”, says Giovanni Lo Nero, Sales Area Manager for Frascold Australia, who adds: “Using a battery of compressors, placed between the receiver and the exhaust of the medium-temperature compressors, ensures a significant increase in efficiency at high external temperatures while reducing the consumption of medium-temperature compressors.”
“We are proud to have contributed to the introduction of such an innovative technology in Australia”, comments Joel Middleton, from MB Refrigeration, who adds: "Frascold is one of our long-standing partners: when our company was chosen as the contractor for this project, we promptly suggested the adoption of their transcritical CO2 components. Frascold’s customer care manifests itself tangibly both through the offer of high-quality solutions with great performances, and a comprehensive service, including counselling in every phase of the project and an excellent after-sale technical support. They also ensured fast delivery, which, in our case, made the difference.”
Giovanni Lo Nero concludes: “We want to thank MB Refrigeration for entrusting us with this exclusive project. It is an important benchmark for Frascold and an exemplary success story that proves the potential of transcritical CO2 in the field, even in critical scenarios. We hope that this installation will help promote the spread of advanced systems in Australia. This market is always in search of alternatives to traditional solutions and is increasingly leaning towards refrigerants that can contribute to the achievement of the country's laudable goal of being a carbon-neutral nation by 2050.”