Heat pumps for the future of comfort
Teon and Frascold, a choice in the name of sustainable innovation
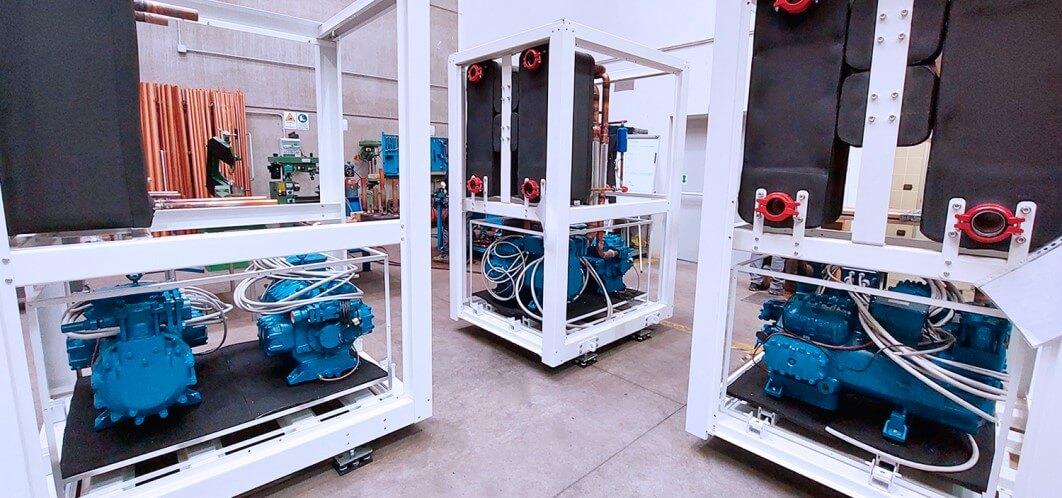
We delve into the topic of geothermal heat pumps and the future of the comfort sector with Ferdinando Pozzani, CEO of Teon.
The comfort sector is called upon to play a crucial role in achieving decarbonisation and energy efficiency goals which are, today, at the forefront of international efforts and, specifically, of the European Union’s Green Deal. Indeed, heating and cooling systems in buildings and industries account for approximately half of the EU’s energy consumption, 75% of which is still generated from fossil fuels.1 A change of gear is needed in order to shake up a sector which is far too heavily focused on traditional systems. With this in mind, Frascold, in partnership with its Customers, is contributing to the sector’s evolution by promoting the adoption of cutting-edge systems. Worthy of note, for example, is the collaboration with Teon, a company engaged in the development, manufacture, and marketing of water-water heat pumps for the residential and industrial sectors, based on the R600a refrigerant which has a low environmental impact.
Let’s find out more about the subject with Ferdinando Pozzani, Teon’s CEO.
Why choose geothermal heat pumps?
At Teon, we believe that heat pumps, and in particular those running at high temperature, are the path to heating and cooling of the future. This is a clean technology, not based on fossil fuels, which moves us in the direction of energy independence. Installing a heat pump, making sure to take advantage of the tax incentives made available to replace traditional boilers, guarantees savings on utility bills of up to 70%2, as well as the greatest reliability and safety, with maintenance costs reduced to the minimum. Open or closed geothermal heat pumps, like those offered by Teon, guarantee operation up to 80°C for heating and hot water production, under any climate condition, without losses in performance. In addition, since they extract most of the heat from natural sources, they are highly sustainable and do not produce any harmful emissions, to the benefit of people’s health and the environment.
What are the crucial elements to consider when making a high-quality heat pump?
Of the various factors that really count in making a reliable heat pump, the exchange units and compressors stand out. That is why, for some years now, we have relied on Frascold, which has worked with us in creating our solutions. This collaboration has its origins in sharing the same guiding principles: Made in Italy excellence, sustainability, and a commitment to innovation. Thanks to Frascold’s input, we have been able to diversify our range in order to meet any heating or cooling need, from residential to commercial and industrial. Furthermore, we are proud to be the only ones on the market to offer a smart heating solution which is compatible with radiator systems that are found in most buildings today. Together with Frascold, we have embarked on a path of growth and recognition in the market of sustainable comfort, with solutions with piston and screw compressors from the ATEX series for hydrocarbons. What we particularly appreciate about the collaboration with Frascold is the constant dialogue with the team and the knowledge of being able to count on the know-how of a leading company in terms of technologies dedicated to hydrocarbons, as confirmed by the completeness of the range of ATEX-certified compressors.
Over the years, we have worked together on numerous projects. Amongst these, for example, the one in an office building in Assago, near Milan, stands out. The Customer was looking for a solution with a lower environmental impact, whilst ensuring superior performance, reduced consumption, and the quietest operation. The challenge was met by replacing the old, highly polluting, diesel boiler with five geothermal heat pumps using R600a and with two compressors in cascade for each machine, for a total thermal power of 1.3 MW. Overall, five CXH01 70-264 AX compressors and five CXH51 125-468 AX compressors were used for the project. Thanks to this new system, the Customer reduced its heating costs by approximately 58%.
2 Comparison done with traditional, oil-fired boilers